Overcoming Common Challenges in Defense Industry Casting
From Concept to Casting: We’ve Got the Capacity
The defense industry demands the highest standards in casting. Components must reliably perform under extreme conditions, so the casting process needs to be precise and consistent. This is crucial because defense equipment cannot fail in critical moments. Challenges like complex part geometries and stringent quality standards pose unique hurdles for casting in this sector.
Identifying Key Challenges in Defense Industry Casting
Casting for the defense industry poses unique challenges that require precise attention to detail and high-quality execution. One major hurdle is meeting stringent quality standards. These parts often need to withstand extreme conditions, which means that any flaw, even a minor one, can jeopardize the entire operation. Achieving this level of quality demands exact tolerances and thorough testing to ensure parts are both durable and reliable.
Complex part geometries also present significant challenges. Many defense components have intricate designs requiring great detail and accuracy. This complexity can make the casting process more demanding, requiring sophisticated techniques and skilled craftsmanship to ensure each part meets strict specifications. The complexity often impacts production timelines, as more detailed work is usually more time-consuming to produce correctly.
These challenges directly affect production and delivery schedules. Casting these parts involves extra checks and balances to ensure every piece aligns with defense requirements. Any delay in achieving the necessary quality can push back delivery dates, affecting timelines and possibly disrupting supply chains. To counteract these impacts, companies often need to implement special workflows that prioritize accuracy while maintaining efficiency.
Material Selection for Enhanced Performance
Choosing the right materials for defense castings plays a crucial role in overcoming production challenges. Certain materials are favored because they offer the strength and durability necessary for demanding defense applications. Here are some materials commonly used in defense casting:
– High-strength aluminum alloys: These offer a combination of light weight and durability, ideal for components that require ease of transport and strong performance under stress.
– Steel alloys: Known for their robustness and resistance to wear, they are suitable for parts facing high-impact conditions.
– Titanium: Although more expensive, titanium provides exceptional strength-to-weight ratios and corrosion resistance, perfect for demanding environments.
Each material offers distinct advantages that align with specific defense specifications. High-strength aluminum alloys, for instance, deliver reliable performance while keeping components light, which is critical for applications like aircraft. Steel alloys provide the toughness needed for parts that have to endure significant stress or impact, while titanium ensures longevity in applications exposed to harsh elements, such as saltwater.
By selecting materials tailored to the specific demands of defense applications, manufacturers can enhance the performance and lifespan of critical components. This careful selection process not only improves the quality of each cast but also ensures the part meets rigorous defense standards, ultimately supporting mission success.
Implementing Advanced Casting Techniques
Advanced casting techniques are essential for enhancing precision and minimizing defects, especially in the defense industry where quality cannot be compromised. One such technique is computer-aided design (CAD), which allows engineers to create accurate 3D models of complex defense components. With CAD, every detail is mapped out before the casting process begins, ensuring high precision in the final product and reducing errors.
Rapid prototyping also plays a crucial role in refining casting techniques. This method allows for the quick creation of a physical model from a digital design, enabling teams to assess and modify designs before full-scale production. By identifying potential issues early on, rapid prototyping helps reduce waste and ensure parts meet specifications from the start.
Technology like automated casting systems enhances consistency in production. These systems maintain precise control over variables such as temperature and mold flow, resulting in uniform, high-quality outputs. Implementing such technologies speeds up production while ensuring each part meets the exacting standards of the defense industry.
Quality Assurance and Compliance in Defense Castings
Quality assurance is a cornerstone of casting for the defense sector. Rigorous testing methods are necessary to meet industry regulations and ensure each component performs reliably in critical applications. Non-destructive testing (NDT) methods, such as X-ray and ultrasound inspections, allow for thorough examination of parts without causing damage. These methods identify hidden flaws that could jeopardize performance, ensuring safety and reliability.
Ongoing quality assurance processes, including regular inspections and compliance audits, are critical for maintaining high standards. Implementing statistical process controls helps in tracking and analyzing production data to catch and correct any deviations early. This proactive approach can prevent small issues from becoming major problems, thus preserving the integrity of the entire production run.
Ensuring continuous compliance with defense regulations strengthens trust with customers and stakeholders. When components consistently meet rigorous standards, they contribute to safer, more effective defense operations. A robust quality assurance framework ultimately guarantees that parts are reliable and ready for demanding environments.
Conclusion
Navigating the challenges in defense industry casting requires a dedicated approach that combines the right materials, advanced technologies, and rigorous quality assurance practices. Addressing these elements ensures that every component crafted for defense purposes is strong, durable, and reliable. By focusing on minimizing defects and optimizing production processes, manufacturers can meet the tight deadlines and exacting standards of the defense market.
Looking for a sand casting partner that prioritizes quality and precision in every component? At BQC Foundry, we’re committed to delivering reliable parts tailored to your unique defense needs. Connect with us to explore how our expertise can support your next critical project, ensuring safe and effective performance in the field.
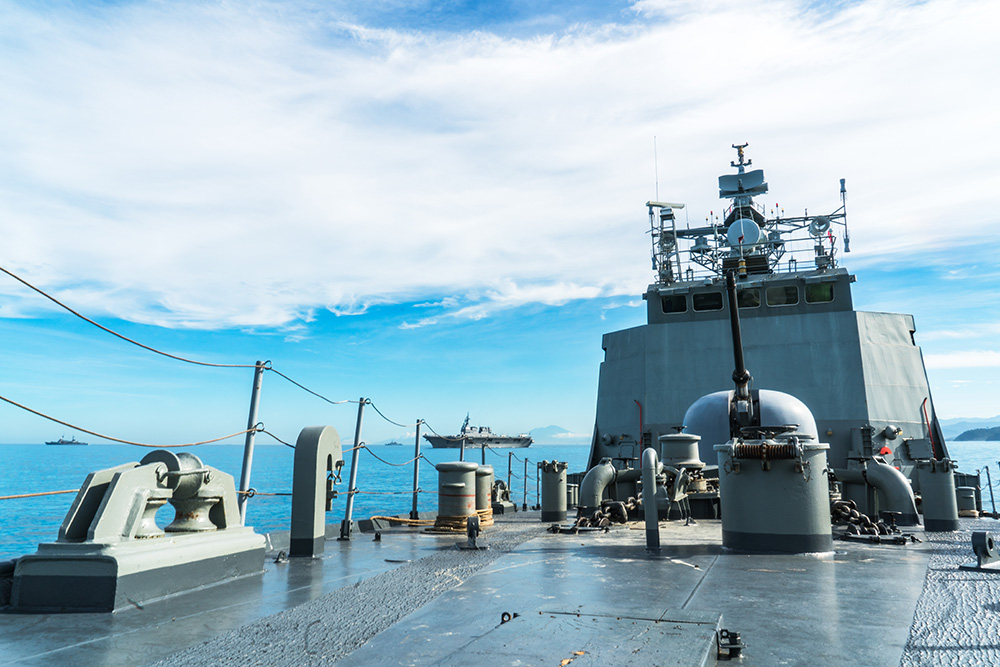