Why Engineering Precision Matters in Aluminum Sand Casting
Engineering Precision in Aluminum Casting
Aluminum sand casting is an intricate process that requires attention to engineering precision. Crafting components with high accuracy is vital because it directly impacts the integrity and performance of the final product. Precision helps ensure that each part functions as intended, which is crucial for applications where reliability is mandatory.
Maintaining precision in aluminum sand casting also leads to significant benefits beyond just the product itself. By reducing waste and minimizing defects, precise engineering contributes to more efficient production processes. This efficiency translates into cost savings and faster turnaround times, which are invaluable in meeting tight schedules and exceeding industry standards.
For industries that rely on aluminum sand casting, such as automotive and defense, precision assures they can depend on parts that deliver consistent performance. Whether it’s components that must withstand high pressures or those needing exact dimensions, precision engineering in casting highlights the intersection of quality and reliability.
The Role of Engineering Precision in Aluminum Sand Casting
Precision in aluminum sand casting is a cornerstone of creating high-quality components. The castings must meet exact specifications to function properly in their eventual applications. When parts are made with precision, they fit perfectly, reducing the chance of failure during operation. This accuracy ensures that each casting maintains its structural integrity, which is vital for industries like automotive and defense where safety and reliability are critical.
A significant aspect of precision casting is the reduction of waste and defects. By engineering each step of the casting process meticulously, manufacturers can minimize the material wasted. This precision not only cuts down costs but also limits the environmental impact by conserving resources. Additionally, a well-engineered casting process significantly lowers the occurrence of defects. Fewer defects mean that fewer components are rejected, which enhances overall production efficiency.
The impact of precision extends beyond the initial manufacturing. Components that are precise and defect-free require less rework and adjustment during assembly, streamlining the entire production line. By investing in precision early in the casting process, manufacturers create a ripple effect that enhances quality and efficiency throughout the lifecycle of the product.
Techniques for Achieving High Precision
Several modern techniques and technologies help achieve high precision in aluminum sand casting. These advanced methods refine every stage of the casting process to ensure accuracy:
– Computer-Aided Design (CAD): CAD software allows engineers to create detailed designs and simulations before physical casting begins. This precision avoids errors that could arise from manual design efforts.
– 3D Modeling: By creating a digital model of the desired component, manufacturers can test fits and functions virtually. This process identifies potential issues before they occur in the physical castings, saving time and resources.
– Automated Mold Making: Mechanizing the mold-making process ensures consistency and accuracy in each mold produced. This automation reduces human error and enhances replication precision.
– Quality Inspection Systems: Incorporating advanced inspection systems, like laser scanners, gives immediate feedback on dimensional conformity, ensuring every casting aligns with design specifications.
By utilizing these techniques, manufacturers benefit from reduced lead times, lower costs, and increased flexibility to make adjustments. CAD and 3D modeling are particularly advantageous as they allow engineers to visualize and test every aspect of a component’s design, ensuring optimal functionality. Automated systems mean that manufacturers can produce higher volumes of precision parts with less manual intervention. These technologies exemplify the strides taken to enhance precision, improving both the production process and the quality of the final product.
Impact on Production Efficiency and Quality Control
Precision engineering plays a significant role in enhancing production efficiency and quality control in aluminum sand casting. When the design and casting processes are highly precise, production cycles become streamlined, allowing manufacturers to meet production schedules with greater consistency. Precision minimizes errors, reducing the number of rejected components, which in turn optimizes the use of materials and time.
Quality assurance processes are also strengthened with precision engineering. Detailed and accurate designs result in parts that meet stringent quality standards more readily, decreasing the need for costly rework or adjustments. Precision engineering facilitates the use of real-time monitoring and automated inspections, ensuring that any deviations from the specified parameters are immediately addressed. This proactive approach ensures that products are not just manufactured on schedule but also meet the quality expectations of demanding industries.
Delivering on-time orders with consistent quality builds trust with clients, a crucial aspect for industries where delays can lead to expensive downtime. With fewer defects and faster production times, companies can allocate resources more effectively, focusing on innovation and expansion rather than remediation, further establishing their reputational reliability in the market.
Industry-Specific Benefits of Precision Casting
Precision casting brings targeted benefits to various industries that rely on aluminum sand casting. In the automotive sector, the demand for lightweight, durable components is ever-increasing. Precision casting allows for the production of complex parts that contribute to fuel efficiency and improved vehicle performance.
The defense industry also benefits significantly from precision casting. Military applications often require parts that must withstand extreme conditions without failure. Through precision casting, components can be reliably manufactured to meet the exacting standards of performance and durability essential in defense operations.
Medical device manufacturing is another sector where precision casting makes a difference. Components used in medical devices must adhere to strict regulatory requirements. Precision ensures that each part is safe and effective, directly impacting patient care and safety.
The oil and gas industry seeks precision casting for producing parts that can endure harsh environments, including corrosive substances and high pressure. Precision casting provides the necessary reliability and longevity these components need to function effectively in such demanding settings.
Conclusion
The importance of precision in aluminum sand casting cannot be overstated. It underpins the quality and efficiency of manufacturing processes and has broad implications across various industries. Precision casting ensures high-quality parts that meet rigorous standards, reducing waste, lowering costs, and enhancing the overall production timeline. Industries from automotive to medical to defense count on these techniques to deliver reliable components that support their operations.
BQC Foundry understands the necessity of precision in crafting components that meet extensive requirements and deadlines. Our commitment to precision casting ensures each part we deliver is built for excellence, offering reliability and performance that our partners can trust. Get in touch with us to explore how our expertise in aluminum sand casting can meet your highest expectations in casting capabilities.
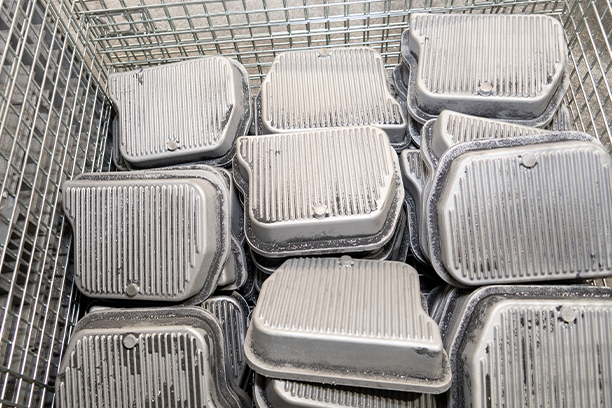