What to Do When Metal Molding Issues Arise in Medical Equipment
Resolving Metal Molding Challenges in Medicine
Metal molding is a critical component in the manufacturing of medical equipment. Molding processes ensure that parts are not only shaped precisely but also maintain high quality and reliability. Imagine a piece of medical equipment failing during a crucial procedure due to a tiny flaw in its construction. It’s a scenario no one wants to face. This is why taking care of every detail in metal molding is vital to delivering reliable performance in medical settings.
Even with the best efforts, challenges can arise in metal molding, impacting the quality of the final product. These issues may stem from minor imperfections in the mold design or inconsistencies in the materials used. Recognizing these common problems and knowing how to address them is key to maintaining the performance and safety of medical equipment. Let’s explore some of the typical issues encountered and how they affect functionality.
Identifying Common Metal Molding Issues
In the world of metal molding, a few common issues tend to pop up time and again, affecting the overall quality of medical equipment. Recognizing these problems early can prevent a lot of headaches down the line.
- Cracks and Fractures: One of the more glaring issues that can occur is cracking. This generally happens if the metal cools too quickly or if too much stress is placed on a particular area. Cracks can weaken the structure, leading to potential failures during usage.
- Distortions and Warping: Sometimes, the final product doesn’t quite match up with the design specifications. This distortion usually results from uneven cooling or improper temperature control during the molding process. Warping can cause alignment issues, making assembly difficult or even impossible.
- Incomplete Fills: When a mold doesn’t fill entirely, it leads to incomplete parts. This might happen due to insufficient pressure or incorrect material viscosity. Incomplete fills can result in weakened areas, reducing the effectiveness and safety of the equipment.
The impacts of these issues on medical equipment can be significant. Cracks may lead to structural failures. Warped parts may cause fit and function issues, while incomplete fills might result in compromised integrity, posing risks during use. Identifying and fixing such issues is crucial for ensuring the reliability of the equipment. Providing solutions to these problems helps maintain the equipment’s performance and longevity while ensuring safety for users and patients alike.
Proactive Measures to Avoid Molding Issues
Preventing metal molding issues in medical equipment requires a thoughtful approach from start to finish. Starting with the right mold design is crucial. A well-designed mold reduces the risk of defects substantially. Think of it like a blueprint for a building—if the design is flawed, the result will never meet expectations. Using high-quality materials also plays a big role. Choose materials that are suited for the environment and conditions in which the equipment will operate. This reduces wear and tear, leading to a more durable product.
Maintenance is your ally in this battle. Regular inspections and upkeep of the molds ensure they remain in top condition. Catching small problems early prevents them from turning into larger, more costly issues. Setting up a routine inspection schedule helps keep things on track, ensuring equipment runs smoothly and efficiently.
Troubleshooting and Correcting Metal Molding Problems
Even with preventive measures, sometimes problems arise. Troubleshooting these issues quickly and effectively is essential to keep operations running smoothly. The first step is identifying the root cause. Observing the symptoms can provide clues. For example, if a part is misaligned, check for distortions that might indicate uneven cooling or incorrect temperature settings.
Once you know the cause, it’s time to fix it. Here are a few steps you can take:
– Adjust Settings: Change the temperature or pressure settings to achieve a more even fill in the molds.
– Check Material Viscosity: Sometimes, the material’s flow can be off due to temperature fluctuations or impurities. Ensure the material is at the optimal temperature.
– Inspect the Mold Design: If issues persist, reconsider the mold design. Sometimes minor tweaks can eliminate repetitive problems.
Remember, correcting problems early saves time and resources, ensuring your equipment remains reliable and safe.
Partnering with a Reliable Metal Molding Service
Finding the right partner for metal molding can make a world of difference. A reputable service provider offers more than just casting parts—they provide peace of mind. Trusting experts with a proven track record ensures that your needs are met with precision and care. They bring specialized skills to the table that can elevate the quality of your equipment.
Such partnerships are invaluable because they know the ins and outs of the industry, often providing insights you might not have considered. They keep up with latest technologies and industry standards, which translates to better quality and efficiency for you. This allows you to focus on what matters most—ensuring your medical equipment operates flawlessly.
Your Go-To Solution for Metal Molding
To maintain high standards in medical equipment manufacturing, it’s important to have partners you can rely on. The process of metal molding is complex, but navigating it with a skilled service provider’s support can make all the difference. They understand the nuances of what makes a good mold and stay ahead of potential problems. Investing in such a partnership ensures your equipment meets both safety and performance expectations, providing you with the confidence that your products are of the highest standard.
For assistance with your metal molding needs, BQC Foundry is here to help. Understand the benefits of working with a trusted metal molding service that ensures high-quality outcomes in the medical field. Check out our capabilities to learn how we can support your equipment manufacturing projects with precision and expertise.
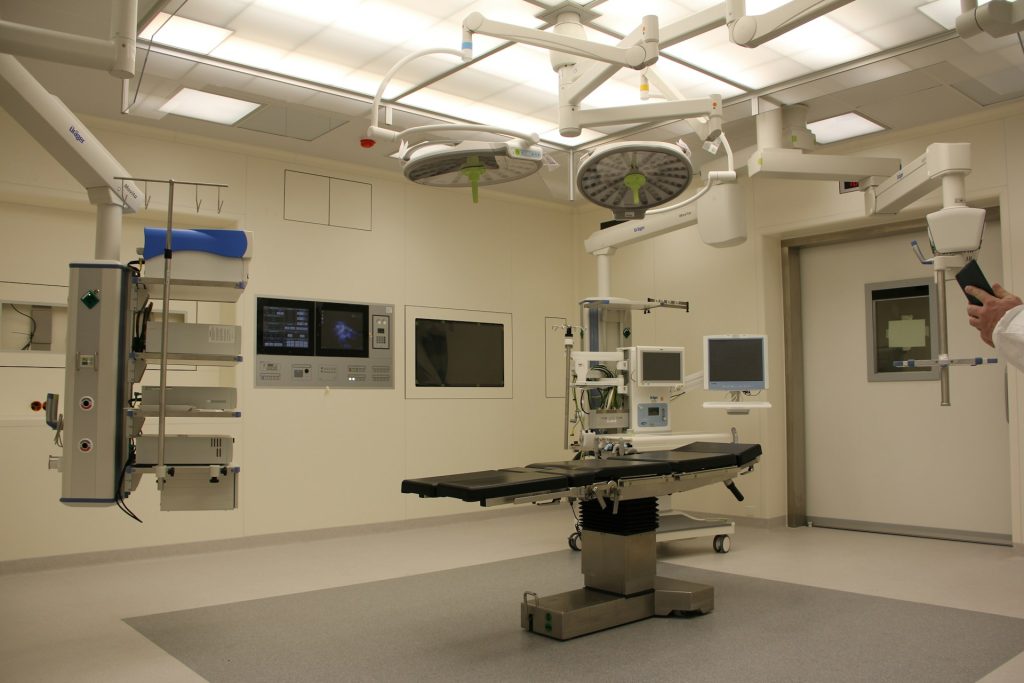