Aluminum Castings for Electrical Components
Aluminum castings play a crucial role in the electrical component industry. They help create efficient, durable, and reliable parts that keep our electronic devices running smoothly. Whether you’re dealing with consumer electronics or industrial machinery, aluminum proves to be an ideal material for various electrical applications.
One reason for aluminum’s popularity is its excellent conductivity and lightweight nature. Unlike other metals, aluminum offers the perfect balance between strength and weight, making it a preferred choice for electrical components. It also handles corrosion well, which is essential for parts exposed to harsh environments.
In addition to its natural properties, aluminum is highly versatile in casting. Modern casting techniques have made it possible to produce complex shapes and intricate designs, which are often required in advanced electrical devices. This blend of material strength and advanced manufacturing ensures that aluminum castings meet the high standards demanded by the electrical industry.
The Importance of Aluminum Castings in Electrical Components
Aluminum is an ideal material for electrical components for several reasons. First, its excellent conductivity ensures efficient energy transfer, which is crucial in any electrical device. It allows for quick and reliable power flow, making sure that electrical systems work smoothly.
An important factor is aluminum’s lightweight nature. When used in components like connectors and housings, it helps reduce the overall weight of electrical devices. This is especially beneficial in applications where weight matters, such as portable devices and electric vehicles.
Aluminum castings play a pivotal role in enhancing the efficiency and durability of electrical devices. Castings allow for the production of complex shapes that other manufacturing methods can’t achieve easily. This means designers can create parts that fit perfectly with other components, improving the overall performance and lifespan of the device.
Better efficiency reduces heat loss in electrical systems, ensuring devices run cooler and last longer. Additionally, aluminum’s resistance to corrosion is vital for components exposed to various environmental conditions. This durability ensures that electrical devices remain reliable over time.
Benefits of Using Aluminum Castings for Electrical Components
There are many advantages to using aluminum castings in electrical components. These include:
– Lightweight: Aluminum is much lighter than other metals, making it perfect for parts where weight is a concern.
– Corrosion Resistance: Aluminum naturally resists corrosion, which is crucial for components exposed to harsh environments.
– Good Conductivity: With excellent electrical conductivity, aluminum ensures efficient energy transfer, critical for any electrical device.
– Versatility: Aluminum can be cast into complex shapes, allowing for intricate designs that fit specific needs.
Common electrical components made from aluminum castings include:
– Housings: Lightweight and durable, aluminum housings protect sensitive parts from damage.
– Heat Sinks: Aluminum heat sinks efficiently dissipate heat, keeping devices cool and preventing overheating.
– Connectors: Aluminum connectors ensure reliable connections between different parts of an electrical system.
These examples show how aluminum castings improve the performance and lifespan of electrical components. By offering a blend of strength, lightness, and excellent conductivity, aluminum castings help create better, longer-lasting electrical devices.
Technological Advances in Aluminum Casting for Electrical Components
Modern casting techniques have greatly enhanced the properties of aluminum. These advances make aluminum castings more precise, durable, and efficient. For instance, high-pressure die casting allows for the creation of complex shapes with tight tolerances. This means manufacturers can produce detailed parts that fit and function perfectly in electrical systems.
Innovations such as 3D printing have also made an impact. By using 3D-printed molds, manufacturers can produce prototypes quickly and at a lower cost. This speed helps companies refine their designs faster, improving the final product’s quality and performance. Additionally, advances in computer-aided design (CAD) and computer-aided manufacturing (CAM) provide more accuracy and consistency in the casting process.
Real-time monitoring systems are another significant advancement. These systems track temperature, pressure, and other variables during casting. This data helps operators make immediate adjustments, ensuring each casting meets the required standards.
Overall, these technological innovations improve the quality and reliability of aluminum castings. They enable the production of superior electrical components that are both dependable and efficient.
Best Practices for Producing Quality Aluminum Castings for Electrical Components
Producing high-quality aluminum castings requires attention to several best practices. First, precision is key. Ensuring that each mold and casting is made to exact specifications helps maintain consistency and quality across all components. This precision can be achieved through detailed planning and the use of advanced tools.
Quality control is another critical aspect. Implementing thorough quality checks at each stage of the manufacturing process can catch defects early. This prevents faulty components from progressing through production and ultimately reaching the customer.
Regular inspections are also vital. Consistently checking equipment and castings helps identify any potential issues before they become significant problems. This proactive approach keeps production running smoothly and maintains high standards.
A dedicated focus on training staff is equally important. Well-trained employees understand the importance of precision and quality control. Providing ongoing training ensures that everyone is up-to-date with the latest techniques and technologies.
Conclusion
Aluminum castings play an essential role in the electrical component industry. They offer numerous benefits such as lightweight, excellent conductivity, and corrosion resistance, making them ideal for creating efficient and durable electrical parts. Through modern casting techniques and technological advancements, manufacturers can produce high-quality, reliable components that meet the demands of various applications.
Maintaining high standards in aluminum casting involves a combination of precision, quality control, regular inspections, and staff training. By adhering to these best practices, manufacturers ensure that their aluminum castings are of the highest quality.
As the electrical industry continues to evolve, the importance of superior aluminum castings will only grow. Reliable components are crucial for the performance and longevity of electrical devices, and investing in quality aluminum castings is a smart choice.
If you’re looking for top-quality aluminum sand castings tailored for electrical components, BQC Foundry is here to help. Our expertise and advanced technology ensure that your projects are completed to the highest standards, providing reliability and efficiency in every casting.
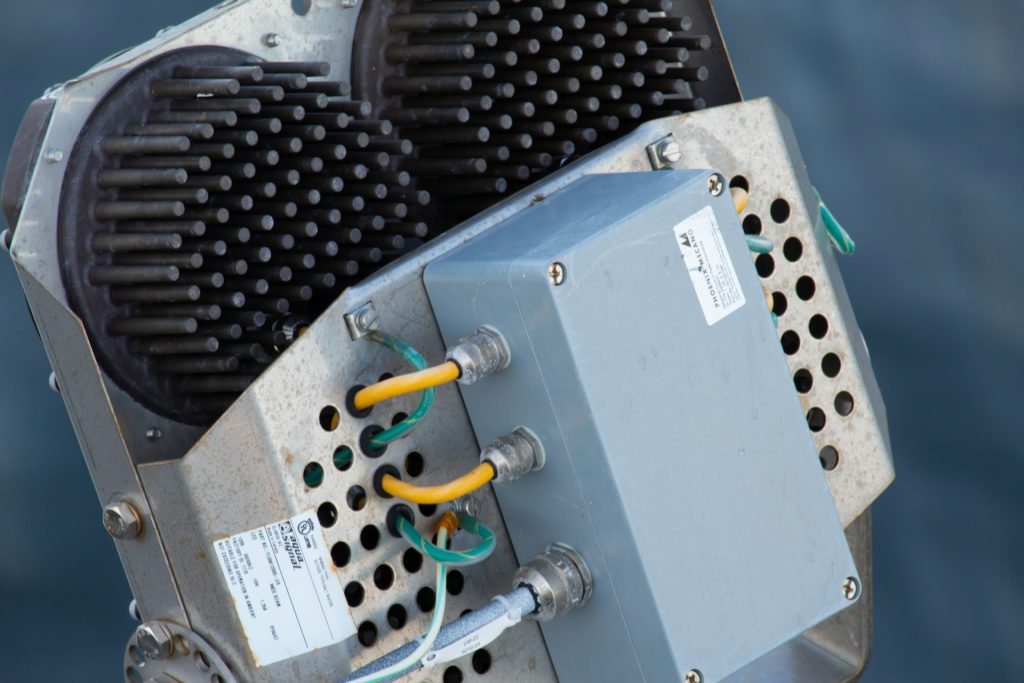