Troubleshooting Guide: Fixing Problems in Aluminum Sand Casting Foundries
Troubleshooting Aluminum Sand Casting Issues
In manufacturing, aluminum sand casting foundries play a key role by crafting parts used in everything from military equipment to vehicles. Yet, like any complex process, it comes with its share of challenges. When issues arise, knowing how to identify and fix these problems can significantly improve production quality and efficiency. Addressing concerns quickly helps maintain steady output and prevents small setbacks from becoming bigger issues.
Consider a scenario where your casting process consistently produces pieces with tiny cracks. Even minor defects like this can slow production or lead to scrapped parts, costing time and resources. That’s why troubleshooting is critical. Through systematic problem-solving, you can uncover errors and keep production lines running smoothly. This guide walks you through common problems found in aluminum sand casting and how to effectively tackle them.
Identifying Common Casting Defects
Aluminum sand casting often encounters various defects which can hinder the final product quality. Recognizing these issues early is key to maintaining high standards. Here are some common problems and how you can spot them:
– Porosity: This involves tiny, often microscopic holes within the casting, usually caused by trapped gases. To identify porosity, inspect the surface of your casting for blistering or uneven texture, and use tools like pressure testing to spot internal voids.
– Cracks: Visible fissures that appear due to stress during the cooling process fall under this category. They often form where the shape of the casting changes quickly, such as corners or junctions. A visual examination is usually sufficient to spot cracks, along with dye penetrant inspection for more refined detection.
– Inclusions: Foreign material trapped in the casting is another defect, often introduced during the molding process. Look for discolored areas or an uneven surface texture, indicating the presence of inclusions.
Understanding how to identify these defects means you’re halfway to solving them. With the right tools and keen observation, you can prevent small issues from becoming bigger roadblocks in your production process.
Effective Troubleshooting Techniques
When problems arise in aluminum sand casting, a structured approach is invaluable for troubleshooting. It’s often best to break down the troubleshooting into manageable steps:
- Inspect Equipment: Begin by checking all machinery for wear and tear, ensuring that tools and components operate smoothly. Malfunctions in the equipment can lead to defects in the final product. Regularly cleaning and calibrating machinery can catch potential problems early.
- Analyze Casting Samples: Examine samples closely. Cut sections from different areas of the casting and inspect for internal issues using methods like X-ray inspections. This helps identify hidden defects that might not be visible at the surface.
- Review Process Parameters: Evaluate your entire casting process. This includes assessing the temperature of the molten aluminum, the speed of pouring, and the condition of the molds. Variations can lead to defects like cold shuts or misruns.
By employing these steps, foundries can address immediate problems and develop a better understanding of how to tweak procedures for optimal results.
Best Practices for Preventive Maintenance
To prevent problems before they arise, a solid preventive maintenance plan is crucial. Referring to a regular maintenance schedule is beneficial for detecting early signs of wear that could turn into significant issues. Here’s a straightforward approach to stay on top of maintenance:
– Scheduled Inspections: Set up regular checks for all equipment. This helps catch small issues before they escalate. Ensure that time is designated for each section of your setup, from sand mixers to mold heaters.
– Maintenance Log: Keep detailed records of all maintenance activities. This log can alert you to equipment that frequently needs repairs, indicating it might be time for replacement or upgrades.
– Training Sessions: Ensure your team knows how to identify signs of equipment stress and can perform basic maintenance tasks. Periodic workshops boost skill levels and awareness.
Preventive measures not only save costs but also ensure you maintain the high standards expected in sand casting operations.
Enhancing Production Efficiency
Boosting efficiency in the casting process involves a mix of modern technology and skilled workmanship. Consider these strategies:
– Implement Advanced Technologies: Use modern software and machinery, like automated casting systems, to streamline operations and reduce error rates.
– Lean Practices: Adopt lean manufacturing principles to minimize waste, improve processes, and ensure that each step in the process adds value. This could involve rearranging production lines or improving communication between departments.
– Regular Training: Regularly update training programs to keep staff informed about the latest techniques and technologies. This enhances productivity and empowers employees to engage with more complex tasks.
Combining improved technology with an organized workforce increases efficiency while reducing defects and delays.
Summing Up Your Casting Troubleshooting Efforts
Consistently high-quality output in aluminum sand casting doesn’t happen by chance. It requires careful planning, regular checks, and a willingness to adapt processes as new insights emerge. By focusing on identifying defects quickly and implementing effective troubleshooting protocols, a foundry can save time and resources.
Regular preventive maintenance is the key to long-term success in casting. It’s about more than just fixing problems—it’s about creating a smooth, efficient process that consistently yields high-quality products. Embrace continuous improvement and stay ready to tackle new challenges, ensuring your casting operations remain efficient, reliable, and top-notch.
If you’re looking for a reliable aluminum sand casting foundry to ensure high-quality parts with fewer defects, BQC Foundry offers exceptional expertise and state-of-the-art solutions. Explore how our comprehensive industrial casting capabilities can streamline your production process and deliver consistent results, helping you meet your project goals efficiently.
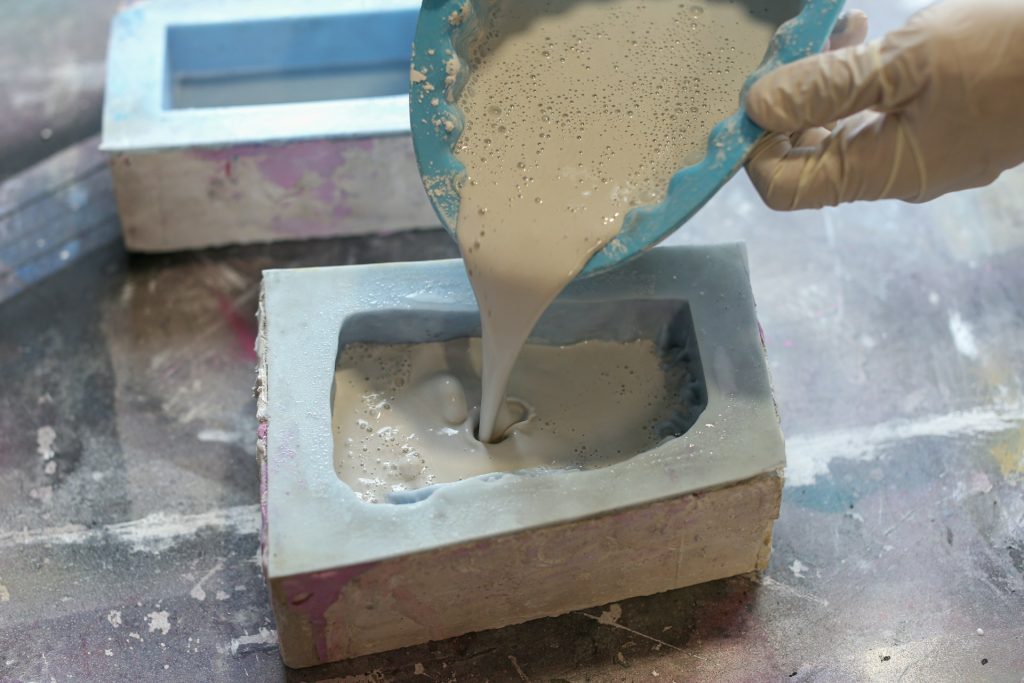